Make Hazard Recognition a Natural Part of Your Daily Work
They say it’s not another checklist, safety program, or training course. So, what is Hazard Recognition Plus™ (HRP)? It’s a way of thinking. One that helps teams spot and manage the hazards others might miss. And while it starts in the mind, it shouldn’t stay there.
With EHSQ software, hazard recognition thinking can become part of your everyday workflow. Workers can be prompted to consider hazards in every process, whether they’re issuing permits, logging a change, or completing an audit. No extra forms, no switching tools. All the questions they need are right there, in the same window.
And it’s all recorded. Because when audit time rolls around, you can’t offer up your workers’ thoughts, but you can show a transparent, fully traceable audit trail.
Where did Hazard Recognition Plus begin?
In the oilfields of Alaska’s North Slope, temperatures drop below -40°F, the sun disappears for months, and the nearest city is hundreds of miles away. In this harsh environment, even routine tasks come with serious danger — hidden spills, fire hazards, equipment failure, and fatigue from endless nights.
When it comes to high-risk environments, they don’t get much more extreme than this. So, it’s no coincidence that Hazard Recognition Plus™ (HRP) was born here after a study into a string of preventable incidents revealed a widespread lack of hazard awareness skills.
Leaders had assumed everyone could spot a hazard, but they’d never taught them how. So, ARCO asked: Can we create a simple, structured way to help people recognize hazards better, in any role and at any level?
That question sparked HRP. Not another paper-based checklist, but a practical mental model grounded in human science. A way of thinking that workers can carry into every task and is designed to sharpen hazard awareness where it matters most: on the job.
Why does traditional hazard training fall short?
Most safety programs assume people instinctively know how to spot hazards. But as many of us have seen firsthand, that’s not always true. Even seasoned workers can overlook obvious risks, especially when human factors come into play.
HRP helps address three of the biggest ones:
Complacency
When tasks feel routine, hazard awareness fades. But conditions can always change. HRP keeps teams thinking critically, so they spot new hazards and plan ahead.
Inattentional blindness
When people focus on one detail, they can miss what’s right in front of them — it’s the “invisible gorilla” effect. HRP teaches workers to pause and scan for hazards beyond the immediate task.
Cognitive bias
We’re wired to make assumptions and take mental shortcuts, like assuming someone else checked the lockout. HRP interrupts that autopilot thinking with a structured process that surfaces hidden risks and prompts smarter questions before work begins.
Building awareness of these factors in daily planning pushes teams from “safety by habit” to “safety by design”, where hazards are actively identified, assessed, and controlled before the job starts.
Because at the end of the day, even the best safety systems will fall short if no one sees the hazard in the first place.
What are the basics of hazard recognition?
HRP is built on Haddon’s Energy Release theory. Put simply, most injuries happen because of uncontrolled energy. HRP makes this concept practical with the Energy Octagon — a clear, visual tool that helps workers quickly spot eight core types of energy around them.
HRP doesn’t stop at identifying hazards. It gives teams a clear, repeatable way to plan safer work using five core questions:
- What is the job?
- What energy is involved?
- Where is the energy going?
- How will we manage the energy for a safe job?
- What are the specific stop-the-job triggers?
These questions help teams plan ahead and think critically, especially during non-routine or high-risk work like maintenance, isolations, shift handovers, and risk assessments. They strengthen the daily foundation of safe operations by adding a layer of critical thinking that safety professionals and frontline teams can carry into their daily work.
How can you use hazard recognition in day-to-day operations?
At TenForce, we know you don’t need more theory. But you do need tools that work the way your teams do. You need a solution that makes the hazard awareness actionable, repeatable, and visible.
That’s why we build hazard recognition questions directly into everyday workflows. So your teams can think critically about hazards right when it matters, without switching apps or windows. It’s not extra work. It’s just how work gets done.
Here’s how teams are putting HRP into practice every day. And how platforms like TenForce help make it part of the workflow.
Built-in risk thinking at every stage of Control of Work
Whether you’re planning hot work, confined space entry, or an isolation, hazard recognition isn’t an afterthought, it’s built into your permit and isolation workflows from the start. No extra forms, no separate tools.
- Hazards are logged and linked directly to permits, isolations, and energy controls, so what’s planned matches what’s happening.
- Stop-work triggers escalate automatically, so red flags don’t get missed.
- Permits reflect real-time conditions, not outdated assumptions, supporting safer decisions in the field.
It’s not just about checking a box, it’s about making sure your controls match the reality on site.
Strengthening process safety with better hazard visibility
Many process safety incidents trace back to missed energy sources, incomplete isolations, or poor shift communication. HRP helps teams look deeper, and TenForce helps make sure those insights don’t get lost.
- During isolations, TenForce prompts teams to think beyond checklists: Where is the energy going? Are we managing all potential sources, not just the obvious ones?
- Isolation points are fully tracked, verified, and linked to the permit.
- Shift handovers can include risk context, not just job status, so incoming teams see the energy state, not just the task list.
TenForce supports critical thinking while keeping your process simple and consistent. And, you automatically get a detailed, time-stamped record, so your HRP thinking is fully traceable and audit-ready.
Closing the loop when someone speaks up
HRP teaches workers to speak up when something doesn’t look or feel right. But what happens to that input? Too often, it’s noted and never seen again. But visibility gaps delay response, and valuable data can be lost before action can be taken.
TenForce closes this gap by giving every level of the organization access to what matters so that field-level insight becomes part of your safety intelligence:
- Workers get a mobile-friendly tool to report hazards, stop-work events, and near-misses right where they happen. All tagged by energy type and risk category.
- Each report can be linked to root cause tracking, so the why behind a hazard is never lost.
- Supervisors can verify controls on the spot — no waiting for paperwork.
- Executives see leading safety indicators through live dashboards, including recurring hazard types, response times, and stop-work trends. This means insights feed directly into your continuous improvement process so you can spot trends, address weak spots, and share lessons learned across sites.
The result? Hazards don’t just get logged. They get seen, acted on, and learned from.
Built for every role. And every risk level
One of HRP’s strengths is its flexibility. It works for everyone from technicians and operators to support staff and contractors. TenForce supports that same flexibility with role-based workflows, granular permissions, tailored risk prompts, and mobile-friendly tools that fit the way your teams actually work and adapt to different roles, sites, and risk levels.
- Field teams get clear, actionable prompts
- Supervisors get oversight without bottlenecks
- Safety leaders get visibility across the whole operation
Turning hazard awareness into action
HRP builds a hazard-recognition mindset at every level, teaching people to see the unseen. But to make it stick, safety thinking needs to be part of the system, not separate from it.
That’s where tools like TenForce come in. By building hazard recognition into daily workflows, TenForce helps make critical risk thinking actionable and auditable across your entire control of work process.
Whether you’re just beginning to explore hazard recognition or looking to strengthen an existing program, it’s worth asking: Are your teams simply documenting hazards, or truly understanding and managing them?
TenForce helps you close that gap. It turns recognition into response. All without adding complexity or slowing teams down. Want to see how? Book a quick demo.
Sign Up for email updates about our latest projects, articles and online events.
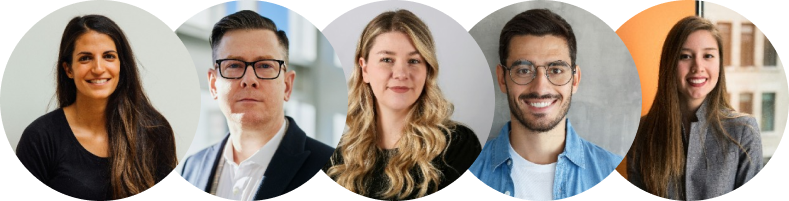
Disclaimer: Hazard Recognition Plus™ is a registered trademark of HSE Global. TenForce is not affiliated with HSE Global or HRP. The above is a description of how TenForce can support companies implementing HRP principles or similar hazard recognition models.